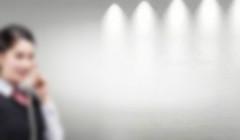
PRODUCTS CENTER
Enquiry hotline
News information
0086-574-88928658

Introduction and requirements of aluminum profiles
Abstract:The following combinations of alloy types and hardness can be used to make aluminum profiles if they meet the requirements of production processing, surface treatment and performance requirements: 6063-T5, 6063-T6, 6105-T5, 6061-T6.
First, aluminum profile performance requirements
A. Aluminum
1. If the combination of the following alloy types and hardness meets the requirements of production processing, surface treatment and performance, it can be used to make aluminum profiles: 6063-T5, 6063-T6, 6105-T5, 6061-T6. Other alloys of the 6xxx series may also be submitted for approval if they meet the requirements of this technical requirement. The thickness of aluminum profiles can not be lower than the following requirements on the basis of meeting the performance requirements:
a. Main aluminum profile: 3.0mm.
b. Cover plate and non-structural decorative strip around the glass: 1.5mm.
c. All aluminum profiles must be high-grade products for construction, and the allowable processing error should meet the "GB/T 5237-Aluminum Alloy Building Profiles Regulations". The material should meet the requirements of "GB/T 3190 - Chemical composition of deformed aluminum and aluminum alloy".
d. All aluminum profiles submitted for review shall be attached with mold drawings to show that they meet the wall thickness requirements of the above materials, and archived.
2. If the combination of the following alloy types and hardness meets the requirements of processing, surface treatment and performance, it can be used to make aluminum sheets or aluminum sheets: 3003-H14, 5005-H14. Other alloys of the 3xxx, 5xxx or 6xxx series may also be submitted for approval if they meet the requirements of this technical specification. The sheet shall meet the requirements of GB/T 5237. The thickness of the sheet shall not be lower than the following requirements on the basis of meeting the performance requirements:
a. Aluminum plate molding component: 3.0mm.
b. Aluminum sheet thickness is 3mm unless specified in architectural drawings. According to the requirements of the use of strengthening measures to ensure that the external flatness of the aluminum plate is not greater than 0.1% or 1.5mm (within 1.5 meters), and the smaller value shall prevail. The thickness of the aluminum plate used for the canopy and ceiling should be 5mm.
c. Cover plate thickness should be 3.0mm.
B. Surface treatment - Aluminum The color and treatment of the aluminum surface shall be consistent with the approved sample within the scope of the aluminum manufacturer is standard color card.
1. Fluorocarbon spraying or other equivalent practice must be approved by the architect.
2. Aluminum exposed outdoors
a. All exterior visible aluminum surfaces shall be coated with Duranar XL at the factory using a fluorocarbon paint based on Kynar 500 fluorinated polymer resin supplied by PPG or other authorized formulations. The exterior curtain wall subcontractor shall submit written authorization to the owner and architect for review prior to painting to certify that the paint formulation and spraying operation meet the requirements.
b. Duranar XL coating consists of three coats and three bakes. PPG primer dry film average film thickness of 5 to 8 micrometers. Duranar paint dry film average film thickness of 25 microns. XL Sun Storm varnish dry film average film thickness of 10 to 20 microns. The total dry film thickness should be at least 40 microns.
c. For example, indented or invisible parts such as internal corners and grooves should also be sprayed as far as possible.
d. Aluminum often has a certain length before cutting and processing. The outer curtain wall subcontractor shall use suitable processing equipment to ensure that the cutting edge is in good condition. Cut edges exposed to outdoor conditions should be treated or sealed to prevent their edges from damaging the coating.
e. Surface treatment
1) A1-Duranar XL (3 paint) or equivalent, light silver, as approved by the architect.
2) A2-Duranar XL (3 paint) or equivalent, dark gray, consistent with architect-approved samples.
3) A3-Duranar XL (3 paint) or equivalent, blue-gray, as approved by the architect.
4) AR1- vertical locking roof system, anodizing and embossing treatment. Consistent with architect approved samples.
5) AR1P- vertical locking roof system with 32% perforation rate and 3mm round hole aperture, anode oxidation and embossing treatment. Consistent with architect approved samples.
6) AR4-Duranar XL (3 coats) or equivalent product, color and texture of AR1.
3. Aluminum is exposed indoors
a. The surface of aluminum is treated with PPG fluorocarbon paint in the factory.
b. Dry film thickness should be at least 60 to 80 microns
c. For example, indented or invisible parts such as internal corners and grooves should also be sprayed as far as possible.
d. The painting operation shall be carried out by the painting factory authorized by the formula factory, and the operation shall strictly comply with the technical requirements for cleaning, priming, coating, and quality control. The exterior curtain wall subcontractor shall submit written authorization to the owner and architect for review prior to painting to certify that the paint formulation and spraying operation meet the requirements.
e. Surface finish 1) A4-Duranar (2 paint) or equivalent, dark gray, as approved by the architect sample. 2) A5-Duranar (2 paint) or equivalent, light silver, consistent with architect-approved samples.
4. Surface paint shall at least meet the requirements of AAMA 2605 - "High performance organic coatings for aluminum profiles and panels" non-mandatory specification, performance requirements and test procedures.
5. Surface paint shall at least meet the requirements of AAMA 2603 - "Colored organic coatings for aluminum profiles and panels" non-mandatory specification, performance requirements and test procedures.
6. Surface paint shall at least meet the requirements of AAMA 2604 - "High performance coloring organic coatings for aluminum profiles and panels" non-mandatory specification, performance requirements and test procedures.
7. The color difference of adjacent components with the same surface treatment method should reach a degree that cannot be detected by the naked eye under normal daylight. External curtain wall subcontractors shall submit samples to reflect the range of color differences for inspection by industrial owners, architects and design consultants.
8. The exterior curtain wall subcontractor shall establish and submit a complete quality control system to ensure that the requirements of this technical requirement are met. The quality control system shall contain documented procedures, procedures, tests, etc. The facade subcontractor shall maintain complete records of inspections, tests and procedures, which shall be submitted to the owner, architect and design consultant on a regular basis. No surface treatment shall be carried out until this quality control system has been reviewed and approved by the owner and architect.
9. Materials which have not been inspected and tested according to the standard, or which have a color difference exceeding the standard color difference range, or which have been rejected by the owner or architect shall not be submitted for examination.
10. The on-site repainting of aluminum must obtain the written permission of the owner. On-site paint repair can only use the "natural air drying" method, as follows:
a. The materials and procedures for field repainting must be in strict accordance with the written instructions of the paint manufacturer.
b. Damaged materials determined by the owner or architect must be replaced.
c. The exterior curtain wall subcontractor must test the complete repainting process on the sample and submit it to the owner and builder for approval. Site repainting shall not be carried out until samples are approved by the owner and architect. The production process of aluminum profiles mainly includes melting casting, extrusion and coloring (the color of this project mainly includes: anodizing, fluorine carbon spraying) three processes. 1, casting is the first process of aluminum production.
The main process is:
(1) Ingredients: According to the specific grade that needs to be produced, the amount of various alloy components is calculated, and various raw materials are reasonably matched.
(2) Smelting: the prepared raw materials are added to the melting furnace according to the process requirements, and the impurities and gases in the melt are effectively removed by degassing and slagging refining.
(3) Casting: Molten aluminum is cooled into various specifications of round casting rods through deep well casting system under certain casting process conditions.
A. Aluminum
1. If the combination of the following alloy types and hardness meets the requirements of production processing, surface treatment and performance, it can be used to make aluminum profiles: 6063-T5, 6063-T6, 6105-T5, 6061-T6. Other alloys of the 6xxx series may also be submitted for approval if they meet the requirements of this technical requirement. The thickness of aluminum profiles can not be lower than the following requirements on the basis of meeting the performance requirements:
a. Main aluminum profile: 3.0mm.
b. Cover plate and non-structural decorative strip around the glass: 1.5mm.
c. All aluminum profiles must be high-grade products for construction, and the allowable processing error should meet the "GB/T 5237-Aluminum Alloy Building Profiles Regulations". The material should meet the requirements of "GB/T 3190 - Chemical composition of deformed aluminum and aluminum alloy".
d. All aluminum profiles submitted for review shall be attached with mold drawings to show that they meet the wall thickness requirements of the above materials, and archived.
2. If the combination of the following alloy types and hardness meets the requirements of processing, surface treatment and performance, it can be used to make aluminum sheets or aluminum sheets: 3003-H14, 5005-H14. Other alloys of the 3xxx, 5xxx or 6xxx series may also be submitted for approval if they meet the requirements of this technical specification. The sheet shall meet the requirements of GB/T 5237. The thickness of the sheet shall not be lower than the following requirements on the basis of meeting the performance requirements:
a. Aluminum plate molding component: 3.0mm.
b. Aluminum sheet thickness is 3mm unless specified in architectural drawings. According to the requirements of the use of strengthening measures to ensure that the external flatness of the aluminum plate is not greater than 0.1% or 1.5mm (within 1.5 meters), and the smaller value shall prevail. The thickness of the aluminum plate used for the canopy and ceiling should be 5mm.
c. Cover plate thickness should be 3.0mm.
B. Surface treatment - Aluminum The color and treatment of the aluminum surface shall be consistent with the approved sample within the scope of the aluminum manufacturer is standard color card.
1. Fluorocarbon spraying or other equivalent practice must be approved by the architect.
2. Aluminum exposed outdoors
a. All exterior visible aluminum surfaces shall be coated with Duranar XL at the factory using a fluorocarbon paint based on Kynar 500 fluorinated polymer resin supplied by PPG or other authorized formulations. The exterior curtain wall subcontractor shall submit written authorization to the owner and architect for review prior to painting to certify that the paint formulation and spraying operation meet the requirements.
b. Duranar XL coating consists of three coats and three bakes. PPG primer dry film average film thickness of 5 to 8 micrometers. Duranar paint dry film average film thickness of 25 microns. XL Sun Storm varnish dry film average film thickness of 10 to 20 microns. The total dry film thickness should be at least 40 microns.
c. For example, indented or invisible parts such as internal corners and grooves should also be sprayed as far as possible.
d. Aluminum often has a certain length before cutting and processing. The outer curtain wall subcontractor shall use suitable processing equipment to ensure that the cutting edge is in good condition. Cut edges exposed to outdoor conditions should be treated or sealed to prevent their edges from damaging the coating.
e. Surface treatment
1) A1-Duranar XL (3 paint) or equivalent, light silver, as approved by the architect.
2) A2-Duranar XL (3 paint) or equivalent, dark gray, consistent with architect-approved samples.
3) A3-Duranar XL (3 paint) or equivalent, blue-gray, as approved by the architect.
4) AR1- vertical locking roof system, anodizing and embossing treatment. Consistent with architect approved samples.
5) AR1P- vertical locking roof system with 32% perforation rate and 3mm round hole aperture, anode oxidation and embossing treatment. Consistent with architect approved samples.
6) AR4-Duranar XL (3 coats) or equivalent product, color and texture of AR1.
3. Aluminum is exposed indoors
a. The surface of aluminum is treated with PPG fluorocarbon paint in the factory.
b. Dry film thickness should be at least 60 to 80 microns
c. For example, indented or invisible parts such as internal corners and grooves should also be sprayed as far as possible.
d. The painting operation shall be carried out by the painting factory authorized by the formula factory, and the operation shall strictly comply with the technical requirements for cleaning, priming, coating, and quality control. The exterior curtain wall subcontractor shall submit written authorization to the owner and architect for review prior to painting to certify that the paint formulation and spraying operation meet the requirements.
e. Surface finish 1) A4-Duranar (2 paint) or equivalent, dark gray, as approved by the architect sample. 2) A5-Duranar (2 paint) or equivalent, light silver, consistent with architect-approved samples.
4. Surface paint shall at least meet the requirements of AAMA 2605 - "High performance organic coatings for aluminum profiles and panels" non-mandatory specification, performance requirements and test procedures.
5. Surface paint shall at least meet the requirements of AAMA 2603 - "Colored organic coatings for aluminum profiles and panels" non-mandatory specification, performance requirements and test procedures.
6. Surface paint shall at least meet the requirements of AAMA 2604 - "High performance coloring organic coatings for aluminum profiles and panels" non-mandatory specification, performance requirements and test procedures.
7. The color difference of adjacent components with the same surface treatment method should reach a degree that cannot be detected by the naked eye under normal daylight. External curtain wall subcontractors shall submit samples to reflect the range of color differences for inspection by industrial owners, architects and design consultants.
8. The exterior curtain wall subcontractor shall establish and submit a complete quality control system to ensure that the requirements of this technical requirement are met. The quality control system shall contain documented procedures, procedures, tests, etc. The facade subcontractor shall maintain complete records of inspections, tests and procedures, which shall be submitted to the owner, architect and design consultant on a regular basis. No surface treatment shall be carried out until this quality control system has been reviewed and approved by the owner and architect.
9. Materials which have not been inspected and tested according to the standard, or which have a color difference exceeding the standard color difference range, or which have been rejected by the owner or architect shall not be submitted for examination.
10. The on-site repainting of aluminum must obtain the written permission of the owner. On-site paint repair can only use the "natural air drying" method, as follows:
a. The materials and procedures for field repainting must be in strict accordance with the written instructions of the paint manufacturer.
b. Damaged materials determined by the owner or architect must be replaced.
c. The exterior curtain wall subcontractor must test the complete repainting process on the sample and submit it to the owner and builder for approval. Site repainting shall not be carried out until samples are approved by the owner and architect. The production process of aluminum profiles mainly includes melting casting, extrusion and coloring (the color of this project mainly includes: anodizing, fluorine carbon spraying) three processes. 1, casting is the first process of aluminum production.
The main process is:
(1) Ingredients: According to the specific grade that needs to be produced, the amount of various alloy components is calculated, and various raw materials are reasonably matched.
(2) Smelting: the prepared raw materials are added to the melting furnace according to the process requirements, and the impurities and gases in the melt are effectively removed by degassing and slagging refining.
(3) Casting: Molten aluminum is cooled into various specifications of round casting rods through deep well casting system under certain casting process conditions.